How is a book printed?
Our editors have worked on the manuscript with an author, it's been proofread and fact-checked, the cover has been designed by the art department and the journalists are all lined up to review the book. But how does the book actually get printed and bound to become the beautiful object that sits on your bookshelf? We went to Mackays printers in Chatham to find out.
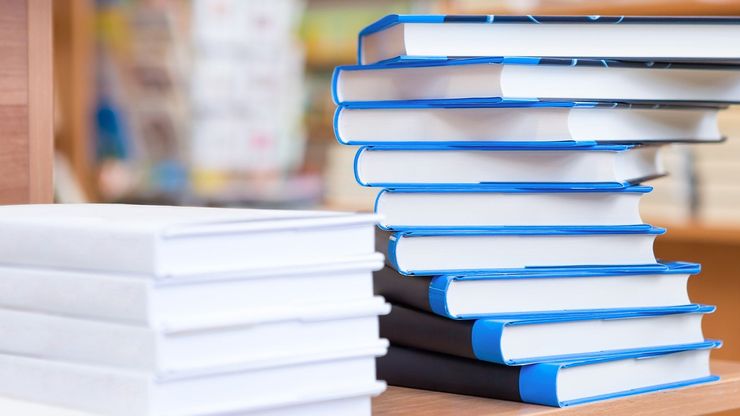
Our editors have worked on the manuscript with an author, it’s been proofread and fact-checked, the cover has been designed by the art department and the journalists are all lined up to review the book. But how does the book actually get printed and bound to become the beautiful object that sits on your bookshelf? We went to Mackays printers in Chatham to find out.
Before we start our journey, we must give you a brief history of web offset lithography printing. First developed in the late eighteenth century, it is based on the principle that oil and water repel one another. An image of the text is transferred photographically onto thin metal, paper, or plastic printing plates. Rollers then apply oil-based ink and water to plates. Since oil and water don’t mix, the oil-based ink won’t stick to the non-image areas of the plate which are water receptive. Only the inked image portion of the plate is then transferred to a rubber blanket cylinder, which transfers the image onto the substrate that is being used.
Stage 1: Preparing the plates
Before printing can take place, metal printing plates of the book must be prepared. Rubber is burnt onto each plate, leaving behind a text image of the book.
Originally, the text was made up of individual pieces of metal type assembled page-by-page, rather than being lasered onto a plate digitally – an immensely skilled and painstaking process. Advances in printing technology to what we have today have enabled the production of affordable and mass market books and revolutionised the dissemination of knowledge and art.
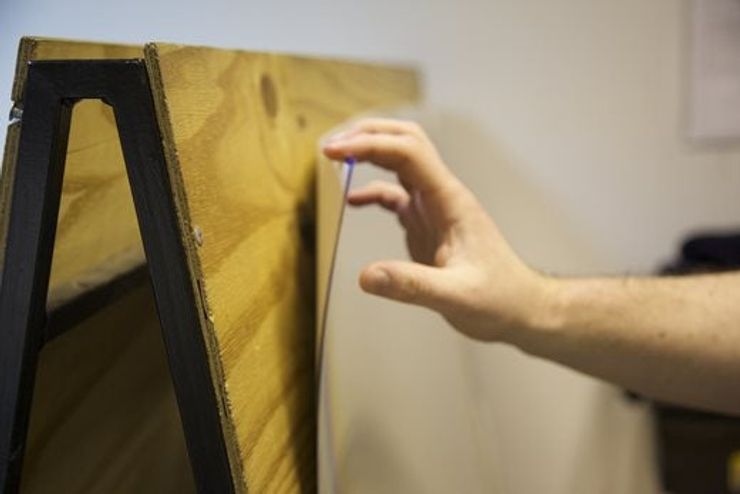
Every printing press has its own specifications that determine how many pages can be produced on a single plate: it's usually sixteen, but it can be eight, thirty-two, etc. The number of pages must be a multiple of this figure, which is why you'll sometimes see blank pages at the beginning or end of books. A 1000 page book, for example, can be broken down into sixty-three sixteen page sections with eight blank pages.
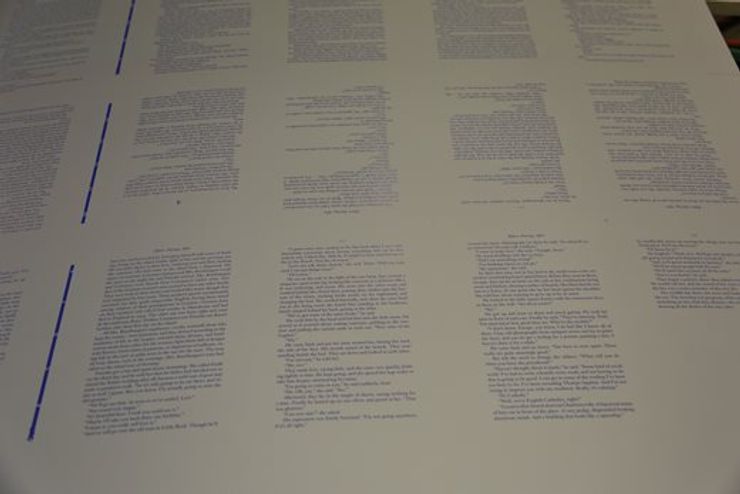
Stage 2: Printing the book
A reel of paper is loaded onto the reel stand of the printing press. The type, weight, colour and width of the paper differ from book to book, and are specified and supplied by the publisher. The reel stand is designed to unwind paper rolls onto the printing lines.
The paper then goes through a chain of rollers, which is called the “in-feed” station. The in-feed station’s main function is to act as a drive to the reel stand, pulling paper off the running reel at the same speed as the running press. It also helps stop creasing and keeps the paper straight as it goes through.
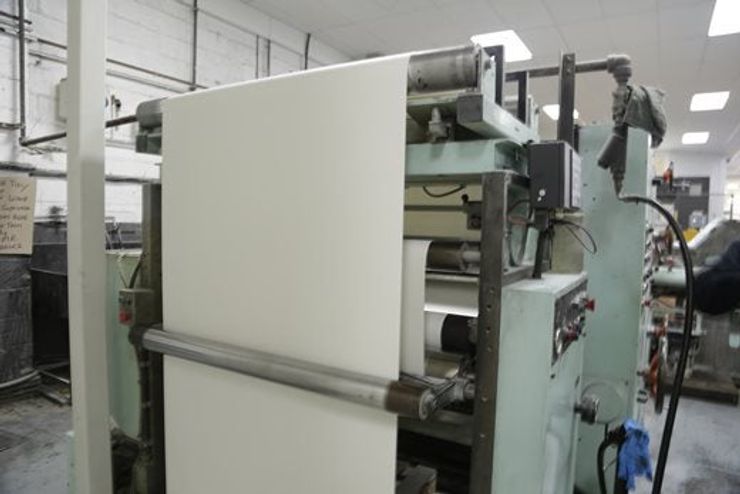
After the in-feed, the running paper reel enters the print units, passing through the inking system, the damping system and the print cylinders. First, the rollers in the inking system transfer ink onto the metal plate. Then the rollers in the damping system spray water onto the plate removing all excess ink from areas that do not need ink. Finally, the print cylinders transfer the inked image area onto a cylinder which then pastes the image onto the paper reel.
null
After the paper reel has passed through the print unit, it will be cut:
null
Folded, stacked and bundled, ready to be bound and cased.
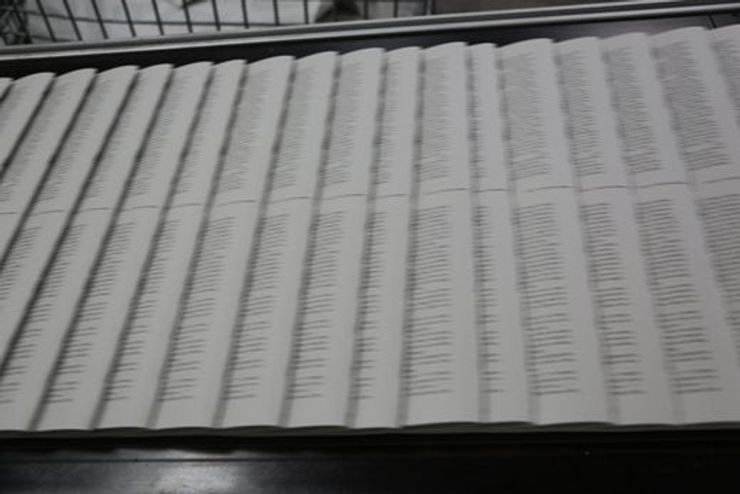
Did you know that a book is printed in sections? Each section has a unique barcode printed on it that will be used when the book is bound and cased with the cover, and is cut off in the final stages.
Stage 3: Preparing the book cover
The book covers are printed at a separate printer as they require specialized printing – that might be coloured foil or embossing, for example.
Two book covers are usually printed on one sheet of paper. They are cut down to size and trimmed.
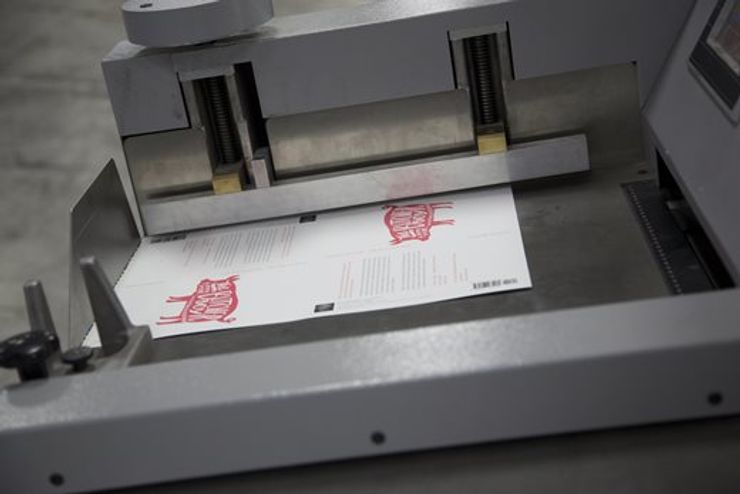
For hardback jackets, cardboard and endpapers are pasted to the covers before the jacket is added to the book.
Stage 4: Adding the cover to the book
As the book is printed in sections, the sections must be correctly stacked (using those barcodes we mentioned) before the cover is glued to them.
Stage 5: The book!
After the book cover is glued onto the printed sections of the book it is trimmed for the last time. And there you have it: the book is printed and ready to go.
The Butcher Boy hot off the press! #picadorclassic
null
All photographs © Maya Robert.