The beauty of the book: an homage to book cover finishes
Charlie Mainprize in Picador’s production team takes us through some examples that show off the marvels of the physical book.
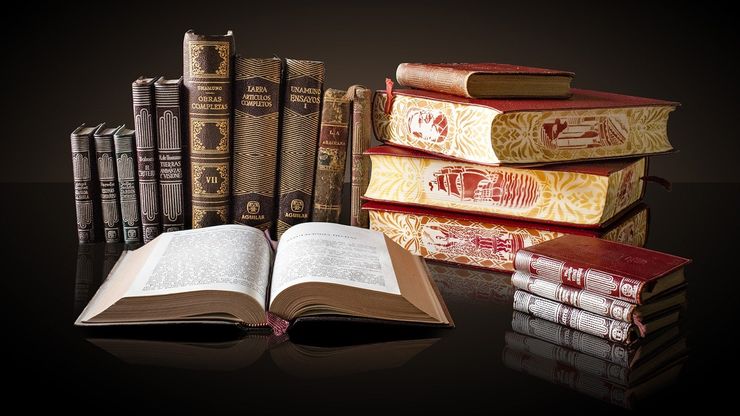
We all know a beautiful book cover when we see one –it can pull you as if by magic from one side of the bookshop to the other with its shiny gold foil or its stroke-me surface. But magic it is not: the clever design and production teams spend hours and days plotting how to make the most of a book's cover so that it does justice to the writing within and still makes a profit overall.
Super matt
This one is a pretty new tool in the kit and it’s all about the texture, making the cover feel like velvet. It’s a tricky one to capture on camera but we’ve done our best here, putting the super matt-finished The Miniaturist by Jessie Burton next to Sunjeev Sahota’s The Year of the Runaways (complete with matt lamination and spot UV) – you’ll have to go into a bookshop to feel them both in the flesh for yourself!
Spot UV
Spot what now? Ultraviolet coating is applied as a think varnish to select points –or spots –on the cover to make them jump out with a high-gloss, vivid shine. When the preliminary designs for Station Eleven by the brilliant Nathan Burton came in, we just couldn't resist adding it on.
Foil
We're all magpies at heart and can't help but be drawn to beautiful, shiny foil. But it must be used sparingly otherwise it stops standing out when you want it to. Designer Jo Thomson used it wonderfully on the cover for The Followers by Rebecca Wait, where it marries perfectly with the subject matter.
Embossing
Embossing is one of the more common cover finishes and is when a part of the design is raised above the rest of the image. Here's the paperback of 2666 by Roberto Bolaño.
Debossing
Embossing's sister, where a part of the image is imprinted into the cover rather than raised above it. The embossing and debossing effects are achieved by applying a die – a metal block with a design etched out in 3D – to the cover or jacket at pressure. Getting the pressure exactly right is a skill; printers make the adjustment manually for each print run according to the thickness of the paper stock and the size of the print run. Dies are created by burning away areas of the metal block in acid baths. Doesn't this picture of Judy Blume's In the Unlikely Event make you want to stroke the image on your screen?
Die cut
Die cutting is when part of the paper is cut away to reveal what is underneath. The die is a little like a heavy-duty metal biscuit cutter. We provide a bespoke design to our printers who have the die made to the exact shape required. The die is applied to the cover at high pressure and cuts directly through the paper, leaving a ‘die-cut' hole behind. There is a limit to how detailed a die cut can be – very intricate shapes tend to be laser cut. The paperbacks of Roberto Bolaño's novels are die-cut, as is the hardback cover of In the Light of What We Know– look closely at the two letter 'o's' in this Vine:
https://vine.co/v/MLvvOzjjtrU/embed/simplePrinting on board
Usually, a hardback book has a dust jacket which has the design printed onto it, and the board underneath is all one colour, with the title and author name on the spine. Sometimes, though, we choose to skip the dustjacket and print straight onto the board. It looks perfect on the hardback of The Kills by Richard House – note the black foil on the title, too!
Endpapers
OK, so this isn't strictly a cover finish, but we had to include it. The endpapers, which are the pages glued to the inside of the cover, are usually white (or the colour of the pages). But every now and then we like to make you look twice. For Wilful Disregard by Lena Andersson we shook it up that little bit more and made them different colours at each end.
Sprayed edges
Another one that isn't specifically about the cover, but... Sprayed edges are exactly what they sound like: the edges of pages are sprayed another colour. The ‘book blocks' – the printed pages of the books which have been bound together – are sprayed with a single Pantone pigment. The process is quite painstaking: small numbers of books (sometimes as few as four at a time) are clamped down in a spray booth. They are then hand-sprayed and left to dry. Our printers can spray around 2000 copies in a day, meaning that we need to allow lots of extra production time for big print runs. Here's the stunning hardback of Tender by Belinda McKeon, with an inky blue on the edges of the pages to match the shocking bruise on the cover.
So there you have it, a brief introduction to the wonderful world of cover finishes and friends.